Druk 3D SLS dostarcza lżejszego i lepszego UAV dzięki usługom produkcyjnym 3D Systems
„Ten proces skutecznie spełnił wymagania dotyczące wagi, a także znacznie zredukował złożoność poprzez tworzenie jednolitych, jednoczęściowych elementów,” powiedział Williams. „Zamiast dodatkowej wagi w postaci złączy i klejów, te części wychodzą z drukarki jako gotowy, pojedynczy element.”
Osiągnięcie niespotykanych wcześniej stosunków wytrzymałości do wagi w przypadku bezzałogowego pojazdu powietrznego T-Hawk dzięki produkcyjnym częściom 3D wydrukowanym przez Paramount Industries, obecnie część usług produkcyjnych 3D Systems.
Początki T-Hawk
Bezzałogowy mikropojazd powietrzny T-Hawk został stworzony w ramach projektu badawczego DARPA, mającego na celu opracowanie niewielkiego pojazdu do prowadzenia wywiadu, nadzoru i rozpoznania w warunkach miejskich. Miał ważyć zaledwie 5 kilogramów, mieć możliwość pionowego startu i lądowania, być łatwy do przenoszenia i obsługi przez żołnierzy, wymagać minimalnego szkolenia oraz być zdolnym do lotu na wysokości do 3000 m.
Honeywell Aerospace, współpracując z AAI Textron Systems, podjęło się realizacji tego projektu, wiedząc, że jego sukces zależy od bardzo szybkiego rozwoju. W tym celu zwrócono się do usług produkcyjnych 3D Systems, poszukując ekspertów w dziedzinie szybkiego projektowania, prototypowania i produkcji części metodą addytywną.
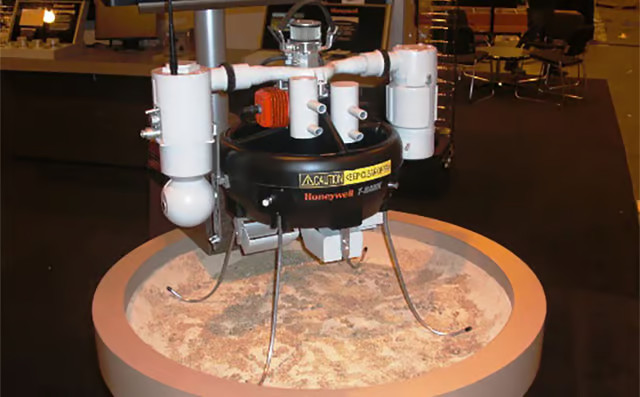
Problemy z tradycyjnymi technikami produkcji
Pierwsze modele prototypowe i testowe projektu zakładały wykorzystanie polimerowych części produkcyjnych, takich jak włókno węglowe czy elementy formowane wtryskowo. Jednak już na etapie wczesnych testów lotu napotkano problemy. Proces projektowania wymagał szybkich iteracji od koncepcji do niskoseryjnej produkcji (LRIP), co było ograniczone zarówno czasem, jak i budżetem.
Wykorzystanie SLS w produkcji T-Hawk
„Każdy moduł sterujący miał maksymalny limit wagi wynoszący 38 gramów,” wyjaśnił Jim Williams, wiceprezes ds. zaawansowanych badań i rozwoju w sektorze lotniczym i obronnym w 3D Systems. „Inżynierowie ramy powietrznej z AAI pierwotnie projektowali je z myślą o włóknie węglowym. Po zapoznaniu się z ich podejściem szybko zauważyłem, że koszty pracy i czas produkcji będą zbyt wysokie i trudne do skalowania. Zamiast tego zastosowaliśmy druk 3D SLS, opracowując techniki budowania modułów jako jednoczęściowych elementów, wykorzystując pustą objętość wewnętrzną, co było możliwe tylko dzięki technologii addytywnej.”
Za pomocą SLS 3D i materiału DuraForm PA zredukowano złożoność procesu i koszty wielu komponentów, tworząc jednoczęściowe moduły o porównywalnych wynikach do włókna węglowego pod względem parametrów aeronautycznych.
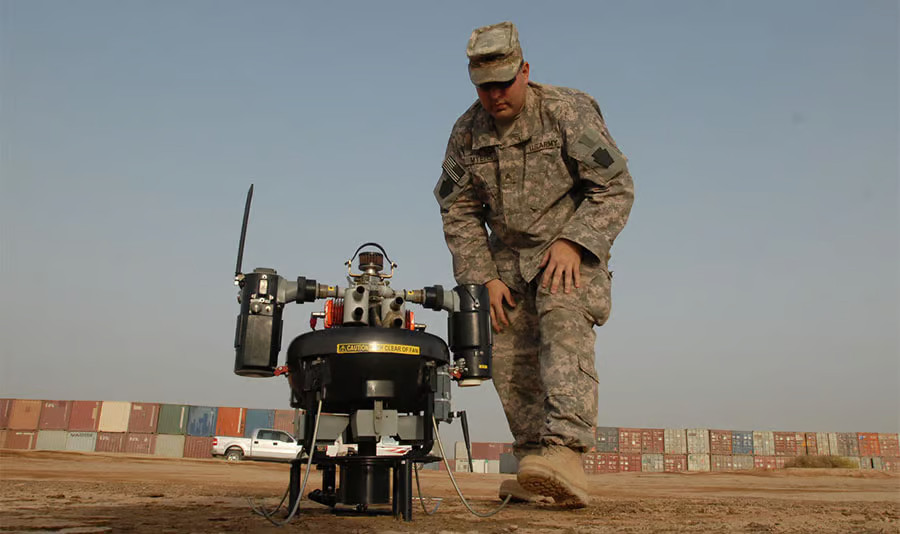
Zastosowanie druku 3D w innych komponentach
Cały proces projektowania i produkcji musiał spełniać wymagania dotyczące wagi, czasu i budżetu. Skomplikowany projekt statora z 13 łopatkami pierwotnie zakładał formowanie wtryskowe, ale narzędzia do tego byłyby zbyt kosztowne i czasochłonne. Zamiast tego opracowano stator z poliuretanu odlewanego z form silikonowych, korzystając z prototypów SLA.
„Dzięki tej technice udało się osiągnąć precyzję i powtarzalność w produkcji ponad 600 systemów przez kilka lat,” powiedział Williams.
Korzyści z produkcji addytywnej
Zespół 3D Systems przeszedł od prototypowania do pełnoskalowej produkcji, wytwarzając dziesiątki tysięcy lekkich i wytrzymałych części. Każdy system T-Hawk zawierał do 76 części wydrukowanych w 3D, co pozwoliło na stworzenie pojazdu zdolnego do lotu z prędkością do 80 kilometrów na godzinę, wykonywania misji dziennych i nocnych oraz oceny zagrożeń takich jak IED.
Całkowicie zmontowany T-Hawk ważył mniej niż 9 kilogramów, mieścił się w plecaku i obsługiwał szeroki zakres misji, co czyniło go niezastąpionym narzędziem dla żołnierzy w terenie.