Wyzwania przemysłu tworzyw sztucznych
Obecnie nasza przemysłowa produkcja może wytwarzać części plastikowe na bardzo dużą skalę i o wysokiej jakości. Niemniej jednak jakość wtryskowanych części plastikowych jest uzależniona od wielu czynników. Od samej formy wtryskowej, przez różne parametry obróbcze, aż po proporcje używanych materiałów plastikowych – nawet najmniejszy błąd może prowadzić do problemów z jakością w całym procesie masowej produkcji.
Na przykład, producenci plastiku zazwyczaj martwią się o ugięcie płyty formy. Takie odkształcenia mogą wystąpić podczas wzrostu ciśnienia i przenikać do formy, osłabiając jej konstrukcję i wpływając na jakość gotowych części. Przeprowadzanie ścisłego monitoringu ugięcia formy jest kluczowe, zwłaszcza w przypadku skomplikowanych części o wąskich tolerancjach. Weryfikowanie wymiarów części w celu śledzenia ugięcia formy może pomóc inżynierom określić status kwalifikacyjny formy na czas. Opóźnienia w weryfikacji formy i kwalifikacji wydajności będą miały wpływ na cały cykl montażu, dostawy i sprzedaży produktów.
Problem tradycyjnych metod pomiarowych
Jednakże, przy użyciu tradycyjnych narzędzi pomiarowych dotykowych, forma wtryskowa i części plastikowe są zazwyczaj mierzone z ograniczoną liczbą punktów pomiarowych, pozostawiając duże obszary niezmierzone. Ponadto części plastikowe mają coraz bardziej skomplikowane geometrie, takie jak głębokie otwory, kieszenie czy krawędzie pod kątem, do których tradycyjne narzędzia nie mają dostępu. W międzyczasie nie można od razu podejmować decyzji o problematycznych obszarach, które nie są natychmiastowo identyfikowane. Na koniec, ze względu na właściwości materiałów, części plastikowe bardzo łatwo się odkształcają, nawet przy niewielkim nacisku na powierzchnię, co utrudnia ich dokładne pomiarowanie. W związku z tym istnieje duża potrzeba szybkiego, wydajnego i bezdotykowego systemu pomiarowego, który przyspieszy proces inspekcji w przemyśle wtrysku tworzyw sztucznych.
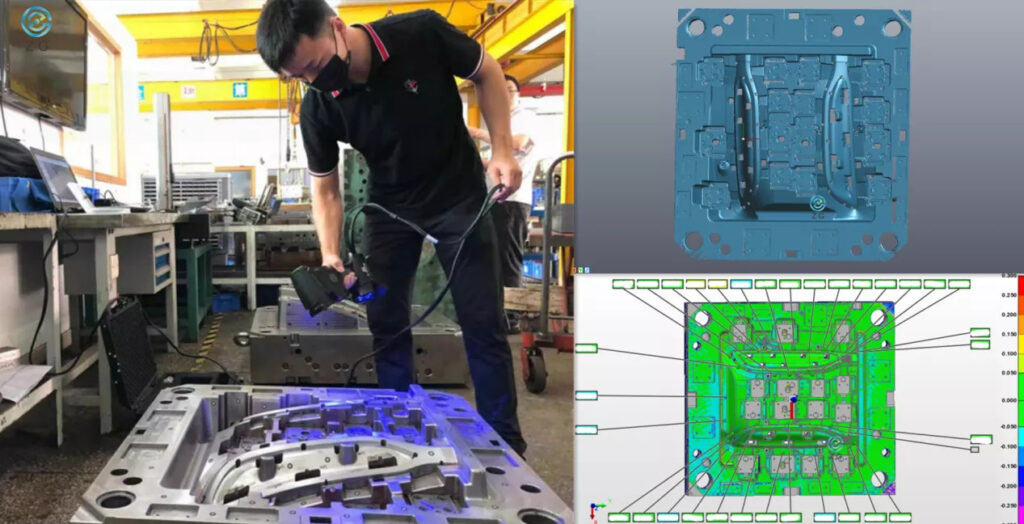
Nowoczesne rozwiązanie
W odpowiedzi na powyższe wyzwania, skaner 3D ZG jest wysoko ocenianym rozwiązaniem bezdotykowym do tego typu inspekcji. Dzięki technologii triangulacji, skanery 3D ZG mogą uchwycić najbardziej dokładne i powtarzalne dane pomiarowe bez dotykania formy i części plastikowych. Dzięki trybom skanowania Standardowym/Single Line/Fine, skanery 3D ZG mogą dostarczyć pełne dane pomiarowe w krótkim czasie. Nawet najmniejsze szczegóły mogą być dokładnie ocenione, na przykład wartości korekcyjne dla geometrii formy oraz parametry maszyny i obróbki. Ponadto dane ze skanowania wielu części mogą być używane do kontroli produkcji oraz analizy trendów, aby zminimalizować odpady i konieczność poprawek.
Inspekcja formy przy użyciu skanera 3D
Formy używane do produkcji części wtryskowych często są tworzone na podstawie zmodyfikowanych danych CAD. Zmiany te obejmują połączenie jednolitych i niejednolitych współczynników kurczenia, dodanie kątów pochylających, linii podziału itd. Najlepsze doświadczenia praktyczne są również włączane w celu zmniejszenia zniekształceń i skręceń części. W związku z tym formy wtryskowe muszą być regularnie utrzymywane w celu niezbędnego odnowienia, aby mogły nadal działać w wymiarach i dokładności, jak zaprojektowano na początku.
Przy użyciu wielomodalnego, wszechstronnego skanera metrologicznego 3D – AtlaScan, który wyposażony jest w 26 niebieskich linii lasera do szybkiego skanowania, dodatkową pojedynczą linię lasera niebieskiego do skanowania głębokich otworów i kieszeni, dodatkowe 5 równoległych niebieskich linii lasera do skanowania detali oraz opatentowaną technologię uchwyty błysków otworów, możemy szybko i dokładnie zeskanować formę wtryskową. Dzięki raportowi inspekcji z mapą kolorów, inżynierowie mogą wyraźnie zobaczyć, czy forma wymaga odnowienia, co nie tylko oszczędza czas, ale także obniża koszty inspekcji w porównaniu do pomiarów manualnych.
Pierwsza Inspekcja Części i Kontrola Jakości
Pierwsza część wychodząca z formy wtryskowej jest krytycznym testem procesu obróbki oraz samej formy. Pierwsza inspekcja części (FAI) to proces dokładnego pomiaru pierwszej części w celu oceny jej kwalifikacji, zarówno pod względem kształtu, jak i wymiarów, względem oryginalnego modelu CAD. W przemyśle wtrysku tworzyw sztucznych, jakiekolwiek odchylenia wtryskowanych części plastikowych od pierwotnego projektu mogą wpłynąć na montaż, wydajność oraz jakość gotowego produktu. To sprawia, że pierwsza inspekcja części (FAI) jest niezbędnym krokiem podczas produkcji części plastikowych.
Jednak nawet jeśli firma ma zatwierdzoną pierwszą część, która jest idealna, a następnie przechodzi do produkcji masowej, może się okazać, że w trakcie procesu coś poszło nie tak i wszystkie części są niezgodne. Takie sytuacje zdarzają się nawet w najlepszych fabrykach, co oznacza, że sama inspekcja FAI to za mało, a kontrola jakości gotowych części powinna być również przeprowadzona skrupulatnie. W przeszłości proces ten wymagał użycia wielu narzędzi pomiarowych i zajmował dziesiątki, a nawet setki godzin. Dzięki skanerom 3D ZG czas ten skraca się do godzin, a nawet minut.
Inteligentny przenośny skaner 3D z niebieskim laserem – RigelScan Elite do FAI
Przy użyciu inteligentnego, przenośnego skanera 3D z niebieskim laserem – RigelScan Elite, niezależnie od tego, czy część plastikowa jest czarna, czy biała, możemy zeskanować ją bezpośrednio bez użycia środka spryskującego i bez kontaktu fizycznego podczas Pierwszej Inspekcji Części (FAI). Co więcej, tylko pierwsza część wymaga manualnej obsługi podczas całego procesu skanowania i inspekcji; Dla pozostałych części w produkcji masowej operacje takie jak wyrównanie danych skanowania z modelem CAD, pomiar wymiarów oraz generowanie raportu mogą być wykonane automatycznie.
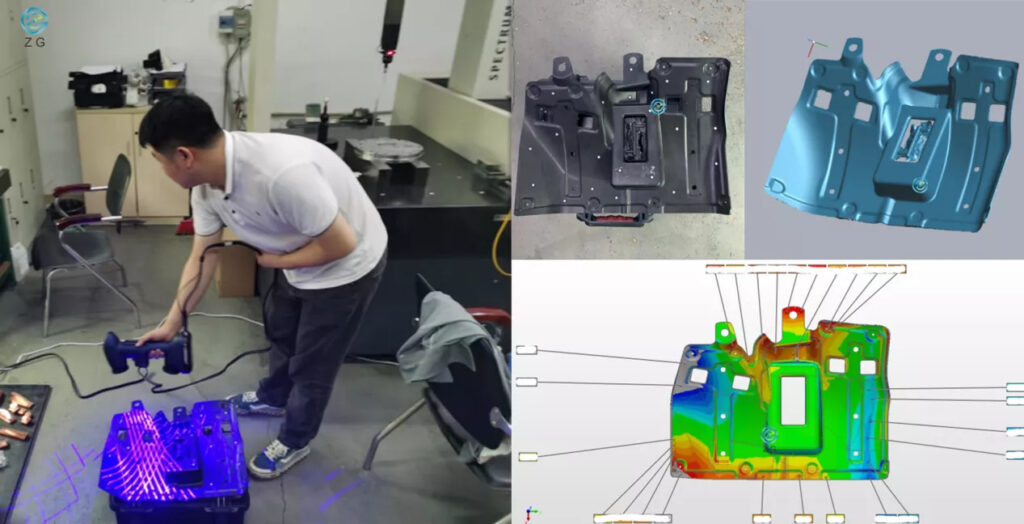
Dzięki łatwemu przechowywaniu i ładowaniu danych skanowania oraz raportów inspekcji mapy kolorów, zużycie i zmiany w procesie produkcji są łatwe do weryfikacji i kontroli. W związku z tym dane 3D pierwszej części i gotowych produktów pozwalają inspektorom nie tylko na niezawodną weryfikację każdego procesu, ale także na monitorowanie różnych procesów produkcyjnych w celu zapewnienia jakości części plastikowych przez cały cykl życia produktu.
Wnioski
Coraz więcej firm wprowadza skanery 3D ZG do swoich działów pomiarowych, nie tylko w celu uzyskania lepszej dokładności pomiarów, ale także w celu zapewnienia kompleksowej oceny całego procesu produkcyjnego poprzez analizę komponentów w pełnym zakresie. Dzięki szybkim inspekcjom i raportom pomiarowym, skanery 3D ZG mogą pomóc producentom części plastikowych zaoszczędzić setki godzin podczas produkcji form, prób produkcyjnych, zatwierdzania pierwszej części i kontroli jakości gotowych części itp., co pozwala uwolnić zasoby inżynierskie, maksymalizować dokładność, zmniejszać liczbę poprawek form oraz skracać czas wprowadzenia produktu na rynek. W ten sposób skanery 3D ZG oferują to, czego żaden inny system nie może zapewnić w przemyśle wtryskowym.
Oprócz wysokiej jakości skanerów 3D, dostępne są również profesjonalne sesje szkoleniowe oraz kursy oparte na materiałach edukacyjnych, takich jak filmy instruktażowe i szczegółowe podręczniki użytkownika dla klientów ZG. Dla ZG Technology innowacja nigdy nie ustaje, podobnie jak jakość i obsługa klienta.