Produkcja przyrostowa (AM) to przełomowa technologia w produkcji mebli, która pozwala na niezrównaną personalizację, elastyczność projektowania oraz zrównoważony rozwój. Spośród różnych technologii druku 3D, ekstrudowanie granulatu stało się metodą wybieraną, ponieważ umożliwia szybkie i opłacalne wytwarzanie elementów w dużej skali, co sprawia, że produkcja mebli gotowych do użytku staje się możliwa.
Studio projektowe Slicelab współpracowało z Grupą Innowacji Aplikacyjnych (AIG) 3D Systems przy realizacji projektu, którego celem było stworzenie koncepcji fotela wypoczynkowego i lampy inspirowanej wizualnym językiem pary lub dymu. Niniejsze studium przypadku bada proces od koncepcji projektowej do powstania dwóch elementów meblowych, które mogły zostać stworzone wyłącznie za pomocą druku 3D z ekstrudowaniem granulatu.
„Kierujemy się projektami, które są unikalne dla druku 3D i mają organiczny charakter. Przekraczamy granice projektowania geometrycznego i granice projektowania dla technologii przyrostowej, aby więcej osób zaczęło korzystać z tej technologii i zobaczyło, co może ona zaoferować.”
— Arthur Azoulai, współzałożyciel Slicelab
Drukowania mebli staje się rzeczywistością
W przeszłości projektanci mebli i producenci często napotykali trudności przy tworzeniu unikalnych, spersonalizowanych mebli. Tradycyjne metody produkcji mebli wymagają dużych nakładów na narzędzia i czasochłonnych prototypów, a także generują znaczne odpady materiałowe. Dodatkowo, produkcja skomplikowanych projektów tradycyjnymi metodami jest często kosztowna lub niemożliwa do wykonania. Ekstrudowanie granulatu w AM oferuje rozwiązania dla tych wyzwań, otwierając możliwości produkcyjne dla innowacyjnych firm, takich jak Slicelab.
Założyciele Slicelab, Arthur Azoulai i Diego Taccioli, tworzą meble i instalacje architektoniczne, wykorzystując zaawansowane metody produkcji, głównie produkcję przyrostową. Sięgnęli po drukarki 3D Titan z ekstrudowaniem granulatu 3D Systems ze względu na możliwość wytwarzania fotela i lampy w jednym kawałku, a także dzięki szybkości i szerokiemu zakresowi materiałów dostępnych do druku.
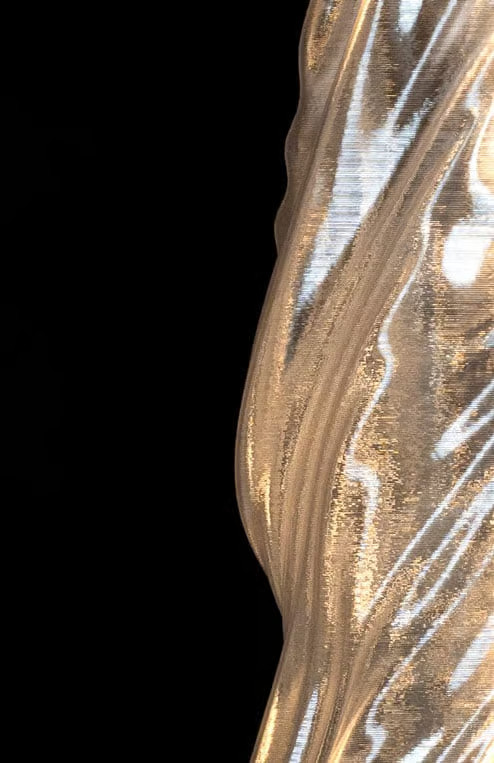
Projektowanie Mebli 3D: Myślenie Poza Schematami
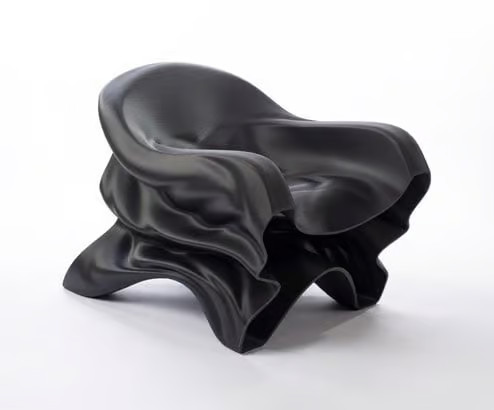
Połączenie estetyki z funkcjonalnością nigdy nie jest łatwe, a Slicelab wiedziało, że chce, aby ten fotel miał organiczny i interesujący profil, który nie tylko wyróżniałby się na tle tradycyjnych mebli, ale także różnił się od innych foteli drukowanych w technologii 3D dostępnych na rynku.
„Inne fotele drukowane w 3D generalnie nie wykorzystują w pełni potencjału technologii przyrostowej. Są drukowane w osi Y, zasadniczo odwracając fotel na bok i wykonując jakąś formę ekstruzji profilu,” powiedział Azoulai.
Zamiast tego, Slicelab zaprojektowało fotel w taki sposób, aby był drukowany z przodem fotela na dole, w kontakcie z płytą roboczą. Takie podejście dało większą swobodę w kształtowaniu ogólnej formy, ale zmusiło ich także do kreatywnego myślenia, aby uniknąć nadmiernych zwisów, które mogłyby utrudnić proces drukowania. A jak w przypadku wszystkich części przyrostowo wytworzonych do użytku końcowego, musiał on mieć odpowiednią wytrzymałość i funkcjonalność fotela, nie uginać się zbyt mocno pod ciężarem.
„Ściśle współpracowaliśmy z zespołem AIG 3D Systems podczas iteracji projektu. Nasza forma przesuwała granice wykonalności druku, równolegle z uwzględnieniem ogólnej struktury,” powiedział Taccioli. „Ich specjaliści pomogli nam udoskonalić projekt na każdym etapie procesu, aby uniknąć nadmiernej elastyczności.”
Od cyfrowego do fizycznego mebla
Wykorzystując wysoką prędkość i wydajność systemów ekstrudowania granulatu Titan, pierwsze wersje fotela parowego i lampy zostały wyprodukowane w ciągu kilku dni. W porównaniu do druku z ekstrudowaniem filamentu, ekstrudowanie granulatu jest do 10 razy szybsze i kosztuje do 10 razy mniej, co umożliwia szybkie i niedrogie iteracje projektowe. Dzięki temu Slicelab szybko otrzymało pierwszy wydrukowany fotel wypoczynkowy, wprowadzając zmiany w projekcie, aby poprawić kąty i wymiary, co sprawiło, że fotel stał się bardziej komfortowy dla szerszego kręgu odbiorców.
Fotel o wymiarach 33” x 31” x 36” oraz lampa o wysokości 67” zostały wydrukowane w jednej części na drukarce EXT 1270 Titan Pellet, mającej objętość roboczą 50” x 50” x 72”. Ze względu na ogromne rozmiary części oraz wymagania estetyczne i funkcjonalne, ekstrudowanie granulatu Titan było jedyną technologią AM, która nadawała się do produkcji tych elementów. Wydruk fotela zajął 25 godzin i wykorzystał 41 kilogramów granulatu termoplastycznego. Wydrukowanie tego samego projektu na drukarce z ekstrudowaniem filamentu zajęłoby co najmniej cztery razy więcej czasu i kosztowałoby dwa do trzech razy więcej w materiałach. Granulaty umożliwiają również ekstrudowanie szerokości do 9 mm, co skutkuje znacznie mocniejszymi częściami niż te wydrukowane na drukarce z ekstruzją filamentu.
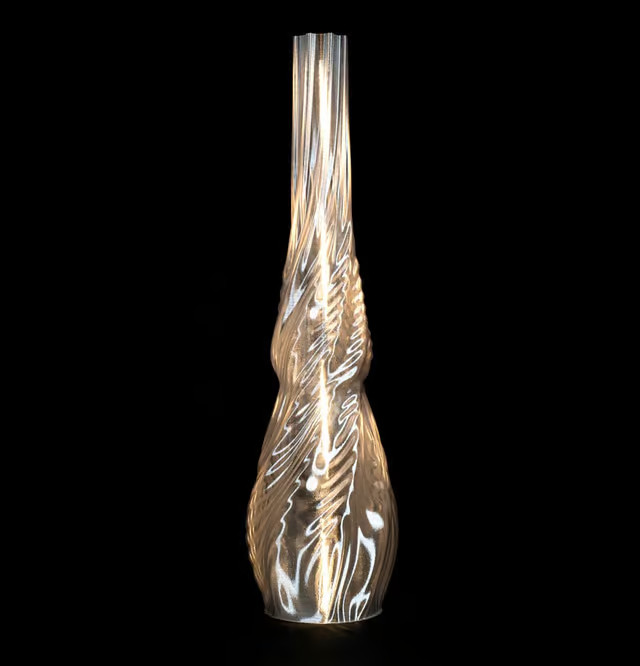
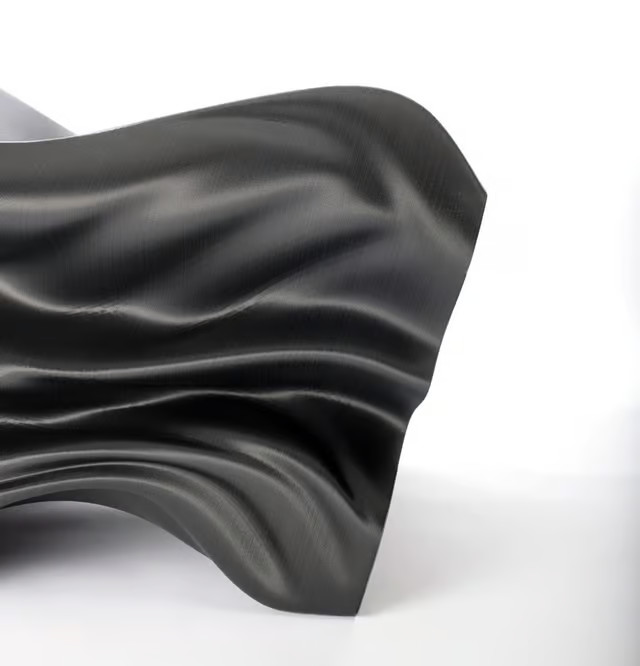
Wyniki drukowania mebli
Drugi wydruk fotela parowego spełnił zamierzony cel projektu. Był wygodny, ładny i wytrzymały. Slicelab otrzymało zainteresowanie tym fotelem od kilku ważnych klientów oraz galerii sztuki.
Usługi AIG 3D Systems pomogły Slicelab uniknąć pułapek typowych dla projektów, które stawiają wyzwania wobec granic technologii AM. Organiczny design fotela parowego skorzystał na ścisłej współpracy między projektantami a ekspertami AM 3D Systems, którzy pomogli nie tylko poprawić wykonalność druku, ale również zapewnić, że fotel będzie funkcjonował zgodnie z zamierzeniami.
Drukarki 3D Titan są wyjątkowo odpowiednie do produkcji niestandardowych mebli dzięki dużemu rozmiarowi konstrukcji, niezawodnej wydajności produkcji „lights-out” oraz technologii szybkiego druku i wytrzymałych materiałów do ekstrudowania granulatu.